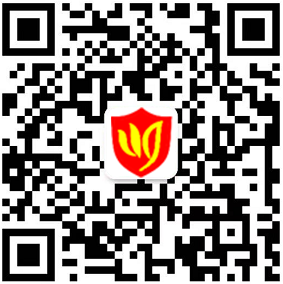
聚氨酯涂料
H.1.1 聚氨酯涂料防腐层的性能应符合表H.1.1的规定。
H.1.2 聚氨酯涂料应有出厂质量证明书及检验报告、使用说明书、出厂合格证等技术资料。用于输送饮用水管道内壁或与人体接触的聚氨酯涂料,应有国家合法机构出具的适用于饮用水的检验报告等证明文件。
H.1.3 聚氨酯涂料应包装完好, 并在包装上标明制造商名称、产品名称、型号、批号、产品数量、生产日期及有效期等。
H.1.4 涂敷作业应按制造厂家提供的使用说明书的要求存放聚氨酯涂料。
H.1.5 对每种牌(型)号的聚氨酯涂料,在使用前均应由合法检测机构,按本标准规定的性能项目进行检验。
H.1.6 涂敷作业应对每一生产批聚氨酯涂料按规定的聚氨酯指标主要性能进行质量复检。不合格的涂料不能用于涂敷。
附录H 聚氨酯(PU)涂层
表H.1 聚氨酯涂料防腐层性能
序号 | 项 目 | 性能指标 | 试验方法 |
1 | 附着力,级 | ≤2 | SY/T 0315 |
2 | 阴极剥离(65℃,48h)(mm) | ≤12 | SY/T 0315 |
3 | 耐冲击(J/m) | ≥5 | SY/T 0315 |
4 | 抗弯曲(1.5°) | 涂层无裂纹和分层 | SY/T 0315 |
5 | 耐磨性(Cs17砂轮,1kg,1000转)(mg) | ≤100 | GB/T 1768 |
6 | 吸水性(24h,%) | ≤3 | GB/T 1034 |
7 | 硬度(Shore D) | ≥65 | GB/T 2411 |
8 | 耐盐雾(1000h) | 涂层完好 | GB/T 1771 |
9 | 电气强度(MV/m) | ≥20 | GB/T 1408.1 |
10 | 体积电阻率(Ω·m) | 1×1013 | GB/T 1410 |
11 | 耐化学介质腐蚀(10%硫酸、30%氯化钠、30%氢氧化钠、2号柴油,30d) | 涂层完整、无起泡、无脱落 | GB 9274 |
H.1.2 聚氨酯涂料应有出厂质量证明书及检验报告、使用说明书、出厂合格证等技术资料。用于输送饮用水管道内壁或与人体接触的聚氨酯涂料,应有国家合法机构出具的适用于饮用水的检验报告等证明文件。
H.1.3 聚氨酯涂料应包装完好, 并在包装上标明制造商名称、产品名称、型号、批号、产品数量、生产日期及有效期等。
H.1.4 涂敷作业应按制造厂家提供的使用说明书的要求存放聚氨酯涂料。
H.1.5 对每种牌(型)号的聚氨酯涂料,在使用前均应由合法检测机构,按本标准规定的性能项目进行检验。
H.1.6 涂敷作业应对每一生产批聚氨酯涂料按规定的聚氨酯指标主要性能进行质量复检。不合格的涂料不能用于涂敷。
条文说明
附录H 聚氨酯(PU)涂层
鉴于目前给水管道工程已有聚氨酯(PU)涂层用作钢管外防腐层的工程实例,为方便应用,将这部分内容列入本规范附录H。
涂敷工艺
H.2.1 表面预处理应符合一列规定:
1 钢材除锈等级应达到现行国家标准《涂敷前钢材表面锈蚀等级和除锈等级》GB 8923-1988中规定的Sa2(1/2)级的要求,表面锚纹深度达到40~100μm。
2 表面温度应高于露点温度3℃以上且相对湿度应低于85%,方可进行除锈作业。
3 除锈合格的表面一般应在8h内进行防腐层的涂敷,如果出现返锈,必须重新进行表面处理。
H.2.2 外防腐层涂敷应符合下列规定:
1 涂敷环境条件:表面温度应高于露点温度3℃以上,相对湿度应低于85%,方可进行涂敷作业。环境温度与管节温度应维持在制造厂家所建议的范围内。雨、雪、雾、风沙等气候条件下,应停止防腐层的露天作业。
2 管材及涂敷材料的加热:需要对被涂敷的管节进行加热时,应限制在制造厂家所规定的温度限值之内,并保证管节表面不被污染。加热方法及加热温度应依照制造厂家的建议。
3 涂敷方法:应按制造厂家的技术说明书进行涂敷,可使用手工涂刷或双组分高压无气热喷涂设备进行喷涂。
4 涂敷间隔:每道防腐层喷涂之间的时间间隔应小于制造厂家技术说明书的规定值。
5 复涂:
1)涂敷厚度未达到规定厚度时,如果未超过制造厂家所规定的可复涂时间,可再涂敷同种涂料以达到规定的厚度,但不得有分层现象。
2)已超过制造厂家所规定的可复涂时间的防腐层,必须全部清除干净,重新涂敷。
6 管端预留长度按照设计要求执行。
附录H 聚氨酯(PU)涂层
鉴于目前给水管道工程已有聚氨酯(PU)涂层用作钢管外防腐层的工程实例,为方便应用,将这部分内容列入本规范附录H。
1 钢材除锈等级应达到现行国家标准《涂敷前钢材表面锈蚀等级和除锈等级》GB 8923-1988中规定的Sa2(1/2)级的要求,表面锚纹深度达到40~100μm。
2 表面温度应高于露点温度3℃以上且相对湿度应低于85%,方可进行除锈作业。
3 除锈合格的表面一般应在8h内进行防腐层的涂敷,如果出现返锈,必须重新进行表面处理。
H.2.2 外防腐层涂敷应符合下列规定:
1 涂敷环境条件:表面温度应高于露点温度3℃以上,相对湿度应低于85%,方可进行涂敷作业。环境温度与管节温度应维持在制造厂家所建议的范围内。雨、雪、雾、风沙等气候条件下,应停止防腐层的露天作业。
2 管材及涂敷材料的加热:需要对被涂敷的管节进行加热时,应限制在制造厂家所规定的温度限值之内,并保证管节表面不被污染。加热方法及加热温度应依照制造厂家的建议。
3 涂敷方法:应按制造厂家的技术说明书进行涂敷,可使用手工涂刷或双组分高压无气热喷涂设备进行喷涂。
4 涂敷间隔:每道防腐层喷涂之间的时间间隔应小于制造厂家技术说明书的规定值。
5 复涂:
1)涂敷厚度未达到规定厚度时,如果未超过制造厂家所规定的可复涂时间,可再涂敷同种涂料以达到规定的厚度,但不得有分层现象。
2)已超过制造厂家所规定的可复涂时间的防腐层,必须全部清除干净,重新涂敷。
6 管端预留长度按照设计要求执行。
条文说明
附录H 聚氨酯(PU)涂层
鉴于目前给水管道工程已有聚氨酯(PU)涂层用作钢管外防腐层的工程实例,为方便应用,将这部分内容列入本规范附录H。
涂层质量检验
H.3.1 涂层质量应按制造厂家标示的涂料固化所需时间进行固化检查,防腐层不得有未干硬或粘腻性、潮湿或粘稠区域。
H.3.2 防腐层外观应全部目视检查,防腐层上不得出现尖锐的突出部、龟裂、气泡和分层等缺陷,微量凹陷、小点或皱折的面积不超过总面积的10%可视为合格。
H.3.3 防腐层厚度应采用磁性测厚仪逐根测量。内防腐层检测距管口大于150mm范围内的两个截面,外防腐层随机抽取三个截面。每个截面测量上、下、左、右四点的防腐层厚度。所有结果符合表H.3.3 中要求或设计要求值为合格。
H.3.4 防腐层检漏应采用电火花检漏仪对防腐层进行100%面积检漏,检漏电压为5V/μm,发现漏点及时修补。
附录H 聚氨酯(PU)涂层
鉴于目前给水管道工程已有聚氨酯(PU)涂层用作钢管外防腐层的工程实例,为方便应用,将这部分内容列入本规范附录H。
H.3.2 防腐层外观应全部目视检查,防腐层上不得出现尖锐的突出部、龟裂、气泡和分层等缺陷,微量凹陷、小点或皱折的面积不超过总面积的10%可视为合格。
H.3.3 防腐层厚度应采用磁性测厚仪逐根测量。内防腐层检测距管口大于150mm范围内的两个截面,外防腐层随机抽取三个截面。每个截面测量上、下、左、右四点的防腐层厚度。所有结果符合表H.3.3 中要求或设计要求值为合格。
表H.3.3 无溶剂聚氨酯涂料内外防腐层的厚度
管材 | 外防腐厚度 | 内防腐厚度 |
钢管 | ≥500μm | ≥500μm |
焊缝处防腐层的厚度,不得低于管本体防腐层规定厚度的80%。 |
H.3.4 防腐层检漏应采用电火花检漏仪对防腐层进行100%面积检漏,检漏电压为5V/μm,发现漏点及时修补。
条文说明
附录H 聚氨酯(PU)涂层
鉴于目前给水管道工程已有聚氨酯(PU)涂层用作钢管外防腐层的工程实例,为方便应用,将这部分内容列入本规范附录H。